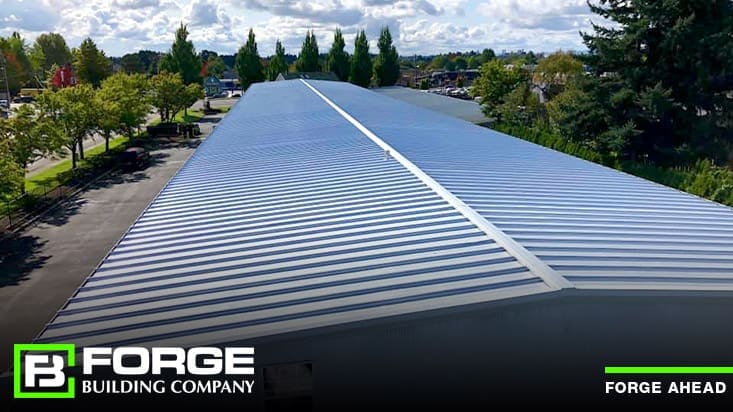
Building a self-storage facility that looks great is important, but to keep customers happy and business booming, you also need to ensure your facility is maintained…especially your unit doors and roof.
Doors
One of the most distinguishing factors of a self-storage facility are the roll-up doors, so it’s important that they be well-maintained! Not only do they contribute to curb appeal, but they are a large part of the tenant experience and can be a safety hazard if left untended.
Doors should be inspected before a tenant moves in, and again after they’ve moved out. Inspection of a roll-up door doesn’t just mean ensuring it looks good but also means it is functioning properly. Here are some guidelines for ensuring your doors look good and function properly.
The Basics
Even when your self-storage units are occupied, there are aspects of your doors that should be inspected regularly. (O'Hearn, 2022) For example, examine the curtain for damage and check the latch for tampering. If the unit has a header draft stop or jamb brush seal, determine if they have excessive wear and replace them if necessary.
Once a unit becomes vacant, there are other items you should inspect before renting it to the next customer.
- First, consider the latch. If it’s worn or appears to have been tampered with, it’s time for a new one. If it’s loose, tighten the nuts on the back.
- Next, assess the bottom seal. Ensure it’s in good shape with no tears. If it is, wipe it down with a protectant such as Armor All, which will help keep it from deteriorating in the sun. If the seal is torn or damaged, replace it with a new one.
- With the door at chest level, ensure the handles are in good condition and securely attached. If the rope is in bad condition or a handle is cracked or missing, replace it.
- Take a look at the door track and weather stripping and make any necessary repairs or cleaning when needed.
- While you’re inside the unit, look for any type of puddles or staining that could give insight into a possible leak. Remove cobwebs, check for signs of pests, and sweep out any dust or debris.
- Finally, check the door guides. Make sure they’re free of debris and wipe them down as needed. If your guides have a runner, inspect it for damage and swap out any broken or torn pieces. If the runner is in good shape, wipe it down with a wax or silicone coating to assist with door operation and protect it from the elements.
- This would also be a good time to ensure all the guide screws are secured tightly to the jamb. If they’re missing or loose, fix or replace them.
The Springs
The most common adjustment to your self-storage doors as they age will be to spring tension. When properly tensioned, the door will open easily. Once it’s about two-thirds open, it should roll up the rest of the way on its own. The springs need more tension if they close too rapidly or require significant force to open. Most doors have a ratcheting mechanism that allows you to make necessary adjustments.
- Using a flashlight or headlamp, roll the door down and look at the springs. If they’re broken or rusted, replace them. If they’re in good shape, lubricate them and check for bird or wasp nests. Clean out any debris that may have accumulated inside the coil.
- Scan the felt tape on the back of the door. If it’s worn, torn, or missing, change it.
- Examine the door brackets to confirm they’re secured tightly to the header. If not, secure them.
The Weather
If you’re in an area that requires wind-locked doors, inspect the brackets and confirm they’re secured to the door. If they are not secure, drill out the old rivets and put in new ones. Some door guides come with a wind-lock insert; ensure they’re also secured now.
- Renting units that meet the requirements of the Americans with Disabilities Act (ADA) requires additional accessibility equipment. Inspect the kit and confirm it’s in good shape, then trade it out as needed.
- If you’re renting vehicle storage or ADA units with door operators, this is a good time to perform any maintenance, check connections, and add fresh batteries to the visor remote.
- Self-storage owners in northern climates do not use salt to melt ice at the doors. This accelerates corrosion and shortens the life of all metal components.
- Inspect paints and coatings. Make sure they stay clean by rinsing them or wiping them off if needed. Most of the paints and coasting used on roll-up doors should last for 15-20 or more years. However, given enough sun exposure, they’ll eventually chalk and fade. If you own a facility that’s 15-plus years old, consider a mass door replacement. Swapping out an entire building’s doors that are nearing the end of their life is a great way to increase curb appeal and support higher rental rates. At Forge, we offer customers either swing or roll up doors. Additional steel angle, wire mesh, and burglar bars are available. Hallway walls can be purchased as flush or ribbed panels. Learn more about our self storage doors and hallways.
The Roof
Protecting your tenant’s property is the main focus of a self-storage facility. That protection includes the structure of the building, and a big part of that structure is the metal roof. It doesn’t matter if you have a traditional, single-story facility or a multi story facility – your metal roof matters.
As self-storage buildings age, roof maintenance and repair become more important and time-consuming. An inspection and maintenance program are an important part of sustaining roof life as well as keeping costly repairs and property claims in check.
With proper inspection and maintenance, a metal roof can last for decades. A good program aims to proactively locate and repair possible leaks while extending the life of the metal panels.
This inspection and care will help you keep your roof in the best possible condition. The most effective examination for metal-roof systems includes four specific areas: the perimeter, the ridge, fasteners, and debris.
To learn more, see Forge Building Company - Metal Building Re-Roofing with Standing Seam Metal Roof Panels
The Perimeter
Perimeter inspections are simple and quick. (Ness, 2015)
- First, walk around the building at the ground level, looking for any loose guttering, if applicable. If your facility doesn’t have gutters, look along the eaves of the building.
- There should be foam closure strips that are typically visible from the ground. These may shrink and erode over time. Missing closures can create several leak points along the walls and doors. The strips can be replaced fairly easily by removing the metal fasteners along the eave strut and lifting the metal panel. After each strip has been replaced, swapping the old fasteners for new fasteners and seals is a good idea.
- After the ground inspection, walk the roof. Ensure the gutters are clean and free of debris, dirt, and sediment. Anything that blocks drainage should be removed. The gutters must drain well to keep water from backing up during rain. Areas of dirt and mud can be displaced using a water hose and a small broom. Look for punctures and corrosion. These can cause serious problems and may require a roof replacement.
- It’s also important to notice any areas of ponded water in the gutters. The low spots that hold water might be caused by mechanical damage or loose gutter straps. Make the appropriate repair to ensure good water flow to the downspouts and lengthen the gutter life.
The Ridge
The ridge is another area for potential leaks.
- Walk along the side of the ridge cap—not on it—visually inspecting the fasteners. Those that are loose or missing should be replaced. Any misalignments found on the ridge cap need to be checked for proper sealant tape. If tape is lacking, apply a sealant to that area.
- If your building doesn’t have a ridge cap, then not only does a maintenance person need to inspect fasteners but must pay careful attention to the creases in the metal panel. These can crack over time and create leaks. They can oftentimes be fixed with a small amount of non-silicone sealant at the point of the fracture.
Fasteners
Effective fastener inspection requires walking each fastener row, one at a time. Fasteners are the single biggest maintenance concern on the older (built in the last 10-20 years) R-panel roof systems. R-Panel roofing has exposed fasteners every few feet. This becomes an issue when the metal roof expands and contracts with hot and cold weather, as the fasteners can become loose. This is where leaks can begin. Not only do loose fasteners allow water into the units, but they can also cause rust and mold. In these screw down roof types, sometimes the seals or seams are not sealed correctly, which can also lead to rust and leakage at your facility. The options are to remove and replace the fastener with a new one or apply non-silicone sealant to the top of the fastener, making certain to completely encapsulate the head.
Standing Seam metal roofing has now replaced R-Panel as an industry standard roof for a few reasons. To start, Standing Seam roofs are 24 gauge, whereas most R-Panels are 26-29 gauge. This means that Standing Seam roof panels are made of thicker metal and are therefore stronger than other panel types. Standing Seam roofs are more resistant to leaks, and this is mostly due to the way that they are designed and installed. This means no water damage to a tenant’s property, which is always a plus.
Debris
Debris on the roof can clog gutters as well as damage metal panels. Certain metal items can strip the Galvalume coating from the panels and dramatically shorten their life. Wire hangers and batteries are two of the biggest culprits, and the end result can be a large area of rust. The longer the metal item is on the roof, the greater the damage will be.
Leak Detection
In the self-storage industry, limited access to units makes leak identification a difficult task. Vacant units should be inspected by the manager immediately following a significant rain. This gives the manager the opportunity to find unreported leaks and can help alleviate problems from tenants in the future. When a leak is identified, it is always advisable to make or arrange repairs as soon as possible.
Schedule
- Newer metal roofs should be inspected every 24 months to ensure the roof is in good condition and to remove all debris. As a roof ages or leaks begin to occur, the inspection schedule should change to every 12 months.
- If possible, keep records and photos of the roof condition. Often, similar issues will occur in the same basic area of the system. Having notes on what’s been done can dramatically shorten the time it takes when pursuing a leak.
- A comprehensive inspection and maintenance plan will help you identify potential leaks before they become a serious issue and ensure your roof lasts as long as it should. Each roof is different and will have its own specific needs. However, a well-defined, timely inspection procedure will keep it watertight for decades.
We all know the customer experience is the backbone of any successful business. At Forge Building Company, we partner with developers that provide the best doors and roofs in the industry. We have over 15 years of experience in this space and will provide all the necessary information needed to help maintain and grow your business.
Let’s begin the discussion on how we can help. Click Contact Us to connect!